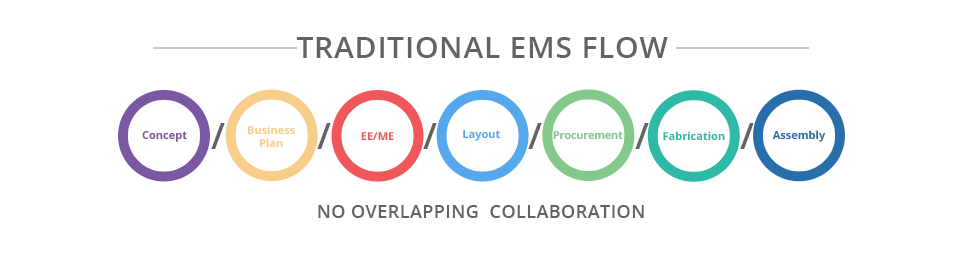
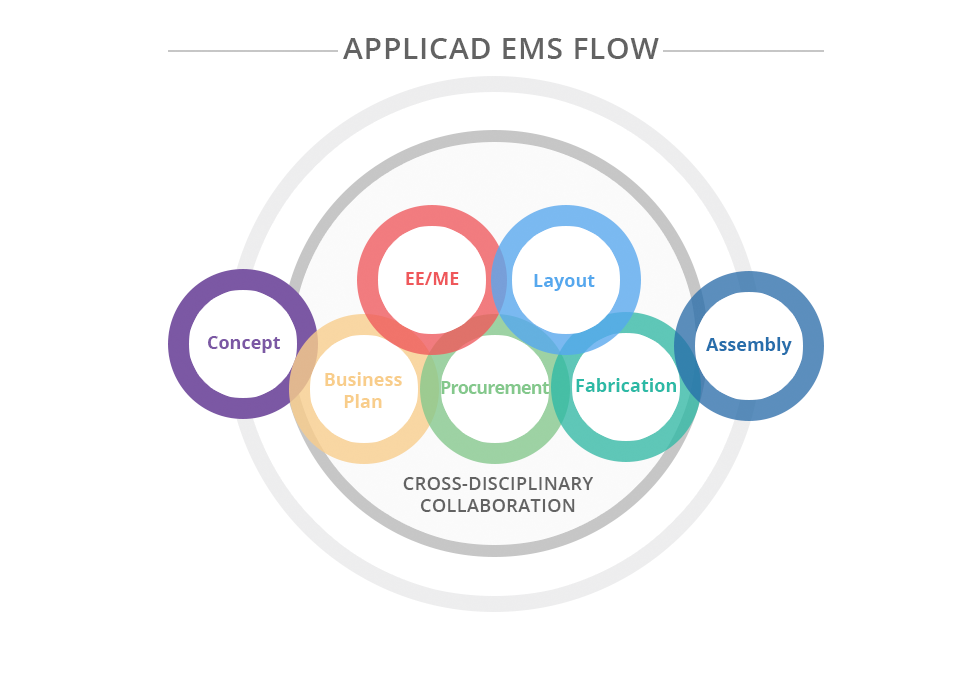
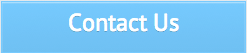
Have any questions? Just call us 732-751-2555
Data comes to us from a wide range of software packages and in wildly varied states. Our specialty is to sift through this raw data and locate potential problems, as well as create a standardized process flow for our shop that leads to efficiency and quality.”
Working with one vendor is much simpler than managing 10 or 20 or more. Letting us be that one point of contact takes a burden off our customers. Our experience and established relationships with suppliers also adds value.”
The electronics component market is a digital minefield – and the traps get moved every day. Our experienced team knows how to navigate through the dangers, to get you the quality materials you need to manufacture a working product.
Our equipment and training allows us to adapt to ever-changing requirements in the electronics industry.”
As a contract manufacturer we have seen wide range of different types of assemblies, from the very simple to the highly complex. This requires flexibility and adaptability. To support this approach we take pride in our well-built and well-maintained state of the art equipment, as well as our technicians who know how to get the most out of that equipment.
Fundamental to our success is our viewpoint that each assembly is unique and must be analyzed on its own. Although past principles and experience assist us, we work to anticipate and address potential problems for each assembly before work begins.
As components get smaller, process windows shrink. We must adapt or we will fail. Regular reviews of materials, equipment, and processes enable us to be vigilant in responding to ever-changing requirements.
We’re constantly tweaking and improving our quality process. And that’s out of necessity. If you blink you’ll miss a half-dozen packaging or process changes.”
Do you think that quality means an inspection at the end of the assembly line? Think again. Quality starts the moment we begin a project and it is woven throughout the entire process, from preparing work instructions through to final inspection, test, and even packaging.
In a rapidly changing industry, the principle of continuous improvement is fundamental to success. Applicad is committed to this principle. In support of this policy we have defined, established, and maintained a quality management system in accordance with ISO standards. This system is ISO9001:2008 certified.